Preventative Maintenance for Universities
School is back in session. As students return to campus, they may discover leaky faucets, broken network connections, and a musty smell from damp carpets. While none of these issues prevent students moving into dorms or starting classes, the already overloaded maintenance team now has a lengthy list of costly repairs to address quickly. And unfortunately, the university did not have a preventive maintenance plan to reduce unexpected repairs.
What happens if you don’t have a preventative maintenance plan for your university?
Most universities respond to issues like the example above with reactive maintenance, a lot of stress, and high costs. This is where a preventative maintenance plan will make a significant impact.
The term maintenance is often associated with equipment failure. However, routine maintenance, known as preventative or preventive maintenance, can help keep universities working efficiently and reduce reactive maintenance.
Preventative maintenance means performing monthly, quarterly, and yearly upkeep on the facility, buildings, and equipment to reduce the chances of things breaking. These routine maintenance tasks include checking physical assets like HVAC systems, plumbing, electrical, networking, flooring, etc. A preventive maintenance plan has many benefits, but some facility managers are overwhelmed with daily tasks and aren’t as proactive as they could be with facility care.
Several issues can arise when a facility lacks a plan for maintenance activities:
Unplanned downtime
Universities depend on the facility and equipment to work efficiently for students and teachers. When things begin to break, it disrupts the learning environment and everyday operations. In the worse cases, classes need to be canceled or students moved to another building.
Costly repairs
Replacing equipment is often more expensive than the cost of planned maintenance. During equipment failure, the facility manager must take a closer look at the situation, source new equipment, and schedule installation. This process can take up to two weeks, depending on the type of equipment. The university will either need to shut down the building or pay expensive rush fees for critical assets like HVAC systems.
Work orders
Setting up a preventive maintenance schedule can reduce the number of unexpected breakdowns and emergency maintenance requests. It will also decrease the cost of purchasing, shipping, and managing parts on a rush basis, which is very expensive over time. Maintenance schedules can also help extend the lifespan of the equipment and facility.
What are the four types of preventative maintenance?
The different types of preventative maintenance are usage-based, time-based, predictive, and prescriptive. Each type has different organization and scheduling, so a facility and maintenance team must pick the appropriate option for their facility.
Usage-based maintenance
This type of maintenance uses the average daily use and environmental exposure to estimate times for inspections and maintenance. Usage-based maintenance is ideal for frequently used equipment.
Calendar/time-based maintenance
Calendar-based maintenance occurs at a scheduled time based on intervals. The maintenance tasks have specific due dates and create work orders as the date approaches.
Predictive maintenance
Predictive maintenance schedules regular maintenance tasks before facility or equipment failure occur. The maintenance team estimates maintenance work based on the condition of the facility and other critical assets. The jobs are then scheduled in advance to avoid unplanned downtime.
Prescriptive maintenance
This type of maintenance works to analyze possible failures throughout the university to reduce risks. Prescriptive maintenance will anticipate items breaking, when, and why. For example, HVAC systems will need new coils installed at the 15-year mark. Prescriptive maintenance notes this need and schedules the new coils before they are likely to break down.
What is proactive maintenance?
Facility managers using a proactive maintenance strategy look at breakdowns as something that can be anticipated and prevented. While similar to the preventive strategy, this method gathers data on all the university assets, from physical buildings to networking systems, and develops a maintenance plan based on early action. The proactive approach also helps maintenance teams find areas where the facility could be more efficient.
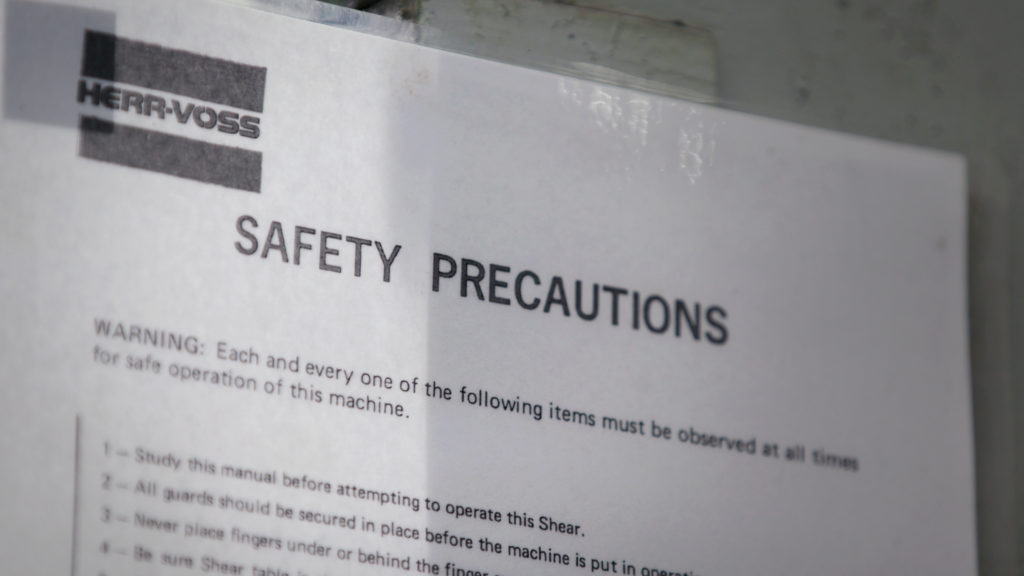
Preventative Maintenance Checklist
Every university should have a preventative maintenance checklist for its maintenance teams. This ensures all planned maintenance is completed on time, even during employee vacations, sick time, or staff changes. The list for each university will depend on the type of buildings, electrical, equipment, and networking systems on campus.
Here are a few items that apply to every university:
- Ensure equipment is clear of debris on a daily basis
- Wipe equipment surfaces
- Regularly inspect HVAC systems
- Check for wear or damage
- Check stairways and walkway railings regularly
- Inspect cabling within classrooms
- Inspect the floor for excessive wear or damage
- Inspect structural building elements at least once per year
- Check and repair building systems (electrical, plumbing, network) at least once per year
- Examine fire detectors twice per year
- Assess external grounds for hazards (parking, common areas)
- Check the roof at least once per year
- Check network connections
- Check WiFi connections
Empower your maintenance team
With a preventive maintenance strategy, facility managers can create a less stressful environment for their maintenance teams. Maintenance technicians will spend less time on reactive maintenance and become more effective. Universities with effective teams turn the maintenance department into an asset, instead of a constant expense.
Deliver continued uptime: Unexpected downtime means facility disruption. Predictive maintenance and monitoring help the facility manager make better decisions for the university’s critical assets.
Managing expectations: A big part of reliability is effective and consistent communication. The team can confidently communicate repairs and timelines with the management team using a computerized maintenance management system.
Secure, reliable budgets: Proactive management reduces surprises and unexpected maintenance costs.
Share information within the team: A CMMS system enables the maintenance team to communicate outstanding work orders and preventative maintenance tasks. This helps when a university is managing different scheduled shifts and locations.
Safety: Sensors connected to the CMMS system can eliminate the need for maintenance technicians to visit hazardous environments for regular inspections.
Does your university have a preventive maintenance plan?
From routine electrical and plumbing repair to systems maintenance, Kroeschell’s experienced team is there to solve complex building management challenges.
Contact Kroeschell to learn more about our innovative facility management solutions.